MAGNETIC LEVEL INDICATOR
The magnetic level Indicator(MLG), also called a magnetically coupled liquid level indicator or magnetic level gauge, is in wide range use throughout the process industries. level Originally designed as an alternative to glass sight level gauges, MLG's are now commonly used in new construction and plant expansions, our magnetic level Indicator are highly accurate & low- maintenance.
They provide redundant, There robust design is ideal for high temperatures, High pressures and corrosive services, Olio instruments Gauges are easy to install and require no additional piping in most application.
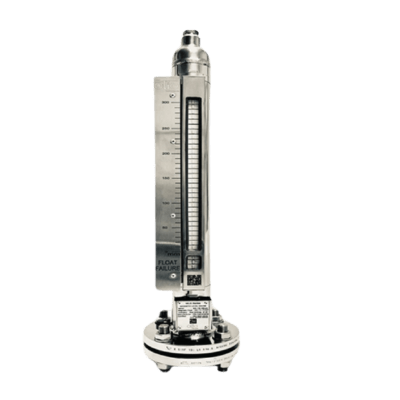
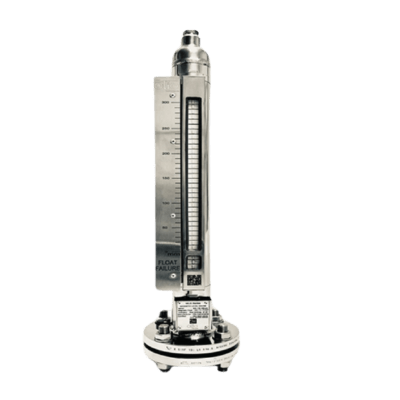
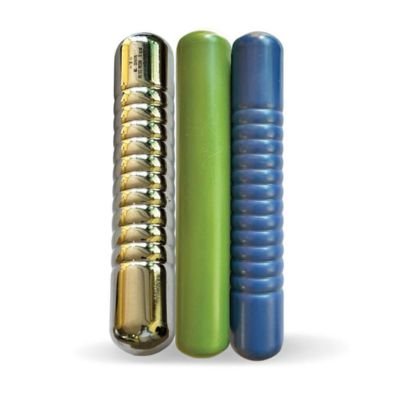
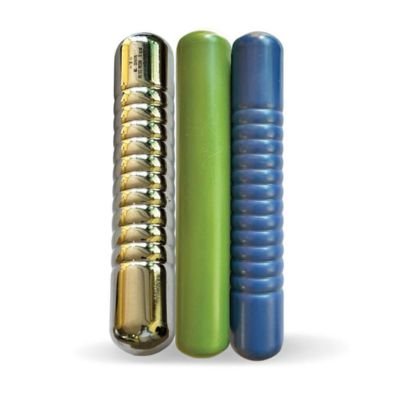
SALIENT FEATURES
- Complies with ASME B31.1 (Power Piping) and B31.3 (Process Piping) design requirements.
- NACE MR0103/0175, Shell DEP Compliances.
- 100% Hydrostatic testing to 1.5x the column rating (typically limited by flange rating).
- Austenitic Stainless-Steel Grades 316/316L, Alloy 20, Hastelloy® C-276, Titanium, Inconel 625/825.
- Special float design to enables to meet Higher pressure, Low specific Gravity applications.
- Indicator encloser IP 67 certified Hermetically Sealed SS316L MOC, Bi-Color anti-vibration flag standard Red/White, (Other colors available on Request).
- Standard width & Wide indicator options available.
- Switch and transmitter option available.
APPLICATIONS AND TECHNICAL DATA
- Interface measurement of liquids.
- Max. Pressure 50 bar for standard versions and up to 150 bar for on request versions. Operating temperatures from -20°c to 200°c.
- Level measurement of particularly aggressive liquids or with pressure and
Visual level indicators for any type of Liquids (S. G. 0.55 min. For the metallic type and 0.88 for the plastic type). temperature not suitable for standard glass tube or reflection indicators Accuracy ± 2 mm.
Special versions for low temperature up to -160°c with anti-frost device and for high temperature up to +400°c.
Max. Length 5.5 meters for metallic type and 3 meters for plastic type.
Version for S.G. < 0.65, on request
- Interface measurement of liquids.
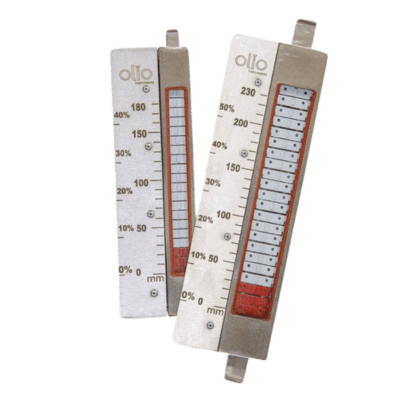
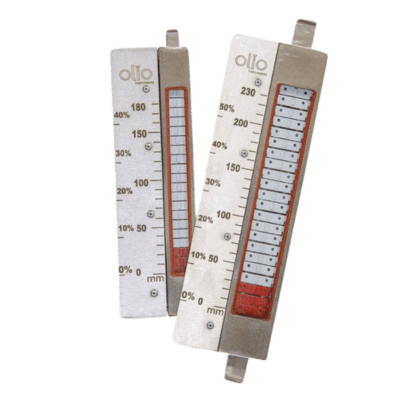
TYPICAL APPLICATION
• Industrial Boilers.
• Chemical Injection skids.
• Storage Tanks.
• Hot Well.
• Boiler Drums.
• Process Vessels.
• Surge Tanks.
• Waste Water Tanks.
• Oil Water Seperators.
• Feed Water Heaters.